
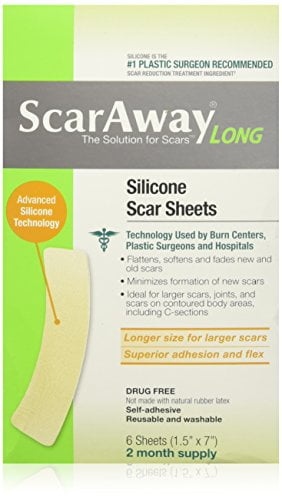
The team then built an apparatus to test the film’s heat conduction. A custom-built flow system further untangled the molecular chains, and spit out the solution onto a liquid-nitrogen-cooled plate to form a thick film, which was then placed on a roll-to-roll drawing machine that heated and stretched the film until it was thinner than plastic wrap. To do this, they dissolved polyethylene powder in a solution that prompted the coiled chains to expand and untangle. Xu and her colleagues looked for ways to untangle polyethylene’s molecular knots, to form parallel chains along which heat can better conduct. Heat has a difficult time flowing through this jumbled mess, which explains a polymer’s intrinsic insulating properties. Normally, the microscopic structure of polyethylene and most polymers resembles a spaghetti-like tangle of molecular chains. In the end, the team was able to fabricate thin films of conducting polymer, starting with a commercial polyethylene powder. The researchers not only had to come up with a way to fabricate heat-conducting sheets of polymer, but they also had to custom-build an apparatus to test the material’s heat conduction, as well as develop computer codes to analyze images of the material’s microscopic structures. “It turns out it was a very arduous process.” “At that time we said, rather than a single fiber, we can try to make a sheet,” Chen says. It soon became clear that, in order for polymer conductors to work for any of these applications, the materials would have to be scaled up from ultrathin fibers (a single fiber measured one-hundredth of the diameter of a human hair) to more manageable films. Their results, published in Nature Nanotechnology, drew the attention of various industries, including manufacturers of heat exchangers, computer core processors, and even race cars. In 2010, the team reported success in fabricating thin fibers of polyethylene that were 300 times more thermally conductive than normal polyethylene, and about as conductive as most metals. “Our bigger vision is, these properties of polymers can create new applications and perhaps new industries, and may replace metals as heat exchangers.”Ĭhen’s co-authors include lead author Yanfei Xu, along with Daniel Kraemer, Bai Song, Jiawei Zhou, James Loomis, Jianjian Wang, Mingda Li, Hadi Ghasemi, Xiaopeng Huang, and Xiaobo Li from MIT, and Zhang Jiang of Argonne National Laboratory. “We think this result is a step to stimulate the field,” says Gang Chen, the Carl Richard Soderberg Professor of Power Engineering at MIT, and a senior co-author on the paper. The team’s results, published in the journal Nature Communications, may spur the development of polymer insulators as lightweight, flexible, and corrosion-resistant alternatives to traditional metal heat conductors, for applications ranging from heat dissipating materials in laptops and cellphones, to cooling elements in cars and refrigerators. In experiments, they found the films, which are thinner than plastic wrap, conduct heat better than ceramics and many metals, including steel. Now MIT engineers have flipped the picture of the standard polymer insulator, by fabricating thin polymer films that conduct heat - an ability normally associated with metals. Think of a silicone oven mitt, or a Styrofoam coffee cup, both manufactured from polymer materials that are excellent at trapping heat.

Polymers are usually the go-to material for thermal insulation.
